난각칼슘의 제조방법
-
소성법 소성 → 건식수화 → 반응 → (미분쇄) → 제품 (난막제거, 살균등의 공정이 필요없음)
-
비소성법 세정 →(분쇄)→난막제거→건조분쇄→미분쇄→살균→제품
계란을 공장에서 집하/세척/검사/할란등의 공정을 거친후, 난황과 난백을 추출하고 나면, 표면상으로 난각이 남게 되는데, 이 난각을 들여다보면, 난막과 난황/난백의 찌거기(흰자/노른자등의 단백질)가 묻어서 남아있다.
(가정에서 계란으로 요리를 해본 사람은, 계란을 깨트려서 사용할때 껍질만 남는지, 아니면 안쪽에 흰자등이 잔뜩 묻어서 남는지 잘 알것이다.)
이후 두가지 방법으로 난각칼슘을 제조하게 되는데, 대표적인 것이 “소성법”과 “비소성법” 이다.
소성법은 통상 1,000℃이상의 고온에서 소성과정을 거치게된다. 이과정에서 대부분의 유기물질이 모두 연소되어 버린다. 난막이나 단백질등의 유기물질이 남아있을 수가 없다. → 무균상태의 고순도 난각칼슘.
비소성법은 소성과정을 거치지 않으므로, 반복적 세척과정이 반드시 필요하고, 공법상 1차 파쇄된 난각에 다량의 물을 투입하여 물속에서 비중을 이용하여 난막을 제거한후 건조/분쇄과정을 거치는데 이 과정에서 유기물질(난막/단백질등)을 100% 완벽하게 제거할 수는 없다.
또한 이과정에서 수차례 발생한 세척수와 일부난막과 단백질등이 섞인 오염수를 처리해야 하는 2차 처리과정과 비용이 발생하게된다. (난각세척후 발생한 오폐수의 경우 악취가 상상을 초월한다.)
이 과정을 환경관련 법규를 준수하면서 제대로 오폐수 처리를 할 경우, 연료를 사용하여 소성로를 운용하는 소성법보다 제조단가가 더 높아질 우려도 많다.
제대로 규정지켜가며 만들면, 제조단가가 결코 저렴하지 않다는것이다.
이러한 과정을 거치더라도 최종 난각분말속에 유기물질이 남아있을 경우 공기중에 노출된 상태에서 쉽게 변질될 우려가 있다. 그래서 비소성 제조법의 경우 통상적으로 마지막에 살균공정이 추가되게 되는데, 보통 열풍을 이용해 살균을 한다. 하지만 어느정도 온도의 열풍을 사용하느냐가 관건인데, 고온에서도 내성을 가지는 균들이 있어서 100% 완벽한 살균이라고 보기는 어려울 것이다.
또한 비소성공정의 특성상 난막이나 난각속의 미량단백질들을 완벽히 제거하는것이 어려운데, 완벽한 살균을 위해서 온도를 높여 고온의 열풍을 분사할 경우 단백질이 탄화될 우려가 있으므로 마음대로 온도를 올릴수가 없다는 것이 딜레마이다. (단백질이 탄화된다는 것은 새까맣게 탄다는 것이다. 새하얀 분말속에 새까만 알갱이들이 섞인다는것은 상품성(백도)를 현격히 떨어뜨리는 것이된다. ) 그럼 제조공장들은 이 단계에서 어떤 선택을 할까?
그럼에도 불구하고 현재 국내를 포함한 해외에서 생산/유통되는 난각칼슘의 절대량은 비소성법에 의존하고 있다.
당국의 규제와 환경단체의 견제가 심한 선진국에서 제대로 설비를 갖추고 비소성난각을 제조하려면 고도의 정제기술과 많은 오폐수 처리비용이 만만치 않을것이다.
하지만 상대적으로 당국의 감시와 규제가 취약한 국가의 경우 절대다수가 비소성법으로 갈 수 밖에 없는 이유는, 오폐수처리등을 신경쓰지않을경우 제조과정이 무척 간단할뿐더러, 제조비용 또한 엄청 저렴해진다는 것이다.
분쇄기와 화학약품 몇가지(표백제,탈취제,방부제)만 있으면 제품생산이 가능하다는것이다.
아래의 <국내 유통중인 난각칼슘의 문제점> 을 읽어보면 현재 국내외의 난각칼슘제품 유통상황을 어느정도 알 수 있을것이다.
- 우리나라에서 논란의 대상이 되고 있는 [1등급계란] 표기란 것이 있다. 마트등에서 흔히 볼 수 있는 깨끗한 표면에 [1등급계란]이란 표식이 인쇄되어있는 제품이다.
- 계란에 “1등급계란”이라는 표기를 하려면 HACCP(위해방지를 위한 사전식품안전관리체계)인증을 받아야하며, 하루5만개이상을 처리할수 있는 집하장과 대당 10억원이 넘는 <계란세척설비>을 갖추어야한다.
- 한마디로 대기업이 아니면 [1등급계란] 표기하기가 힘들다. 계란유통협회와 영세양계농가/유통인들이 대기업과 이 문제를 놓고 맞서고 있다.
- 양측이 맞서는 과정에서 논란의 도마에 오른 것은 바로 계란세척 공정이다. “세척해야된다” 와 “세척하면 않된다”는 의견이 맞서고 있는데, 이건 아직도 정부가 결론을 못내리고 있다.
- 난각에는 미세한 기공이 존재한다. 산소와 탄산가스의 이동통로이다. 알이 숨을 쉬는 것이다.
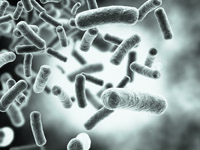
- 또한 계란은 상업적 양계시설 시스템 자체가 고도로 청결을 유지하기는 힘든 구조이며, 산란직후 계란의 표면에는 계변/혈액/분비물등이 묻어있어서 살모넬라등 병원균에 취약한 것이 사실이다. 하지만 계란에는 천연보호막이 있으니 이것이 난각표면의 일종의 코팅층인 <큐티클층>이다.
- 계란유통협회가 주장하는 것은 계란표면을 세척하면 이 큐티클층이 씻겨져버려서 각종 병원균에 오염될 소지가 높아진다는 것이다. 학계에서도 이 주장은 사실인 것으로 인정해주는 분위기이다.
- 하지만 도시의 소비자들이 계분이나 분비물이 남아있는 계란에 얼마나 손이 갈지는 의문이다.
- 참고로 미국도 세척이 의무화이며, EU의 경우도 영내국가 이동시 세척이 의무이다. 이 문제에 대한 해결은 정부로 맡기기로 하자.
- 우리가 여기에서 짚어보아야 할 것은 세척을 한 계란이든, 않한 계란이든 난각칼슘을 만들 때 소성법을 이용해 1,000℃이상의 고온에서 소성시켜버리면, 식중독을 유발하는 살모넬라를 비롯한 세균류는 물론, 알레르기나 변질의 문제를 일으킬 수 있는 단백질이나 유기물등이 전혀 남아있을수 없다는 사실이다.
- 또한, 주기적으로 온국민을 불안으로 몰아넣고, 양계업계를 초토화 시켜버리는 <조류독감 바이러스>의 경우에도 70℃에서 30분, 75℃에서 5분이면 완전 사멸한다. 하물며 바이러스에 노출된 계란이더라도 1,000℃에서 소성시켜버리면 바이러스는 물론 유기물질 자체가 잔류할 수가 없다.
- 이것이 단순분쇄의 비소성법과 확연히 구별되는 소성법만의 빼어난 장점이다.
비소성법 제조시의 위험요소
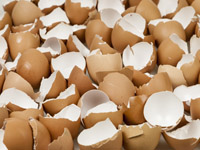
- 대규모 복합 설비를 갖춘 업체를 제외한 대부분의 경우 계란공장에서 난백/난황을 채취한 후 빈난각을 난각칼슘공장으로 보내기전까지 창고등에 쌓아두고 보관하게 되는데 이때 난각내외부에는 난백찌꺼기 등의 단백질이 잔뜩 묻어있다.
- (계란후라이 할때 싱크대에 버려진 계란껍질 상태를 생각해보자.) 가정의 싱크대에 버려진 한두개의 난각은 그렇다치고, 이것이 창고에 몇톤씩 쌓여있으면 어떻게 될까?
- 괞찮을까? 살모넬라등 세균이 번식하지는 않을까? 부패하지 않을까? 고온다습한 여름에는 어떻게 될까?
- 할란후 최단시간에 난각제조 설비에 투입된다고 해도, 산화와 부패를 완벽하게 피하기는 힘들다.
- 이상태에서 비소성법으로 제조된다고 상상해보면...
♦국내산 (대부분 비소성법으로 제조)
- 거의 대부분이 비소성법으로 제조.
- 소성법의 경우 초기 설비투자비용이나, 운용비가 많이 들어 영세한 중소기업이 쉽게 손을 대기 힘듬.
- 무리해서 투자를 하여 소성법 제조시설을 갖추어도, 절대량을 소비하는 라면이나 제과등의 대기업들이 이미 계열사나 관계사등의 형태로 비소성난각 제조시설을 보유하고 있으므로 판매처의 확보가 쉽지않음.
- 소비자(사용공장)입장에서 볼때 선택의 폭이 좁아서, 수입산으로 쉽게 눈을 돌릴 수 밖에 없음.
- 중국산의 저가의 유혹까지 더해질 경우 재고의 여지가 없음.
- 그나마 수요에 비해 공급량이 절대부족하여, 상당량을 수입에 의존하고 있음. (외화유출-연간 3,000억원)
- 국내 식품업계에서는 식용난각칼슘의 상당량을 일본에서 수입해서 사용해왔는데, 제품단가도 비싸고 최근에는 방사능 문제까지 대두되어 그안전성이 의심됨.
- 일본국내 소비처들도, 난각을 납품받을경우 방사능검사서의 첨부를 요구하고 있는 상황임. (이때 제출해야할 검사서나 판정서가 한두가지가 아님)
- 인체에 흡수되어 뼈에 축적되어 골수암,백혈병등을 발병시키는 스트론튬-90의 경우 2013년 7월기준 후쿠시마 원전부근에서 기준치의 160,000배가 측정되었음.
- 스트론튬-90의 경우 일본기술로도 실시간 신속측정이 불가하여, Eurofins Analytics에 의뢰하여 판정을 받아야함. (우리나라의 경우 대형마트의 수입식품 코너에서 휴대용 방사능측정기를 갖다놓고 측정하는 모습을 시연한 후에 "괞찮습니다, 안전합니다"라고 소비자앞에서 현장판정을 내려버림. )
- 또한 국내에 비해 일본의 업계가 훨씬 더 오랜시간동안 고도의 정제기술을 축적한 것은 사실이나 물리적으로만 유기물질을 분리/제거 해서는, 유기물이100%제거 되었다는 보장이 없음.
- 일본식품법상에도 비소성제품의 경우, 알레르기 유발물질로 규정된 난류를 사용하였다고 표기해야함.소성품의 경우는 표기의무 없음.
- 국내에 수입되어 유통되고 있는데, 저가의 어묵이나 햄, 분식류등의 식품에 쓰이는데, 육안으로 볼 때 백도자체는 상당히 우수함.
- 소성품이 아닌 단순분쇄한 비소성품인데도 불구하고 계란 특유의 비린 냄새도 없고, 백도가 아주 우수함. (비소성난각의 경우 백도가 낮고, 계란비린내가 나야 정상임.)
- 겉보기 상품성은 중국산이 아주 뛰어남.
- 분석해 보면 다량의 탈취제와 표백제 및 방부제를 사용했음. - 식품용으로 도저히 쓸 수 없음.
- 무엇보다 유통과정이나 제조과정의 위생적 관리에 대한 담보가 전혀없음.
- 수입업자들이 국내산으로 둔갑시킬경우, 대책이 없음.
- 이러한 정보나 지식이 없어서 모르고 사용하는 업체나 업소도 있을것이며, 알고서도 가격 때문에 사용하는 곳도 있을 것이다.